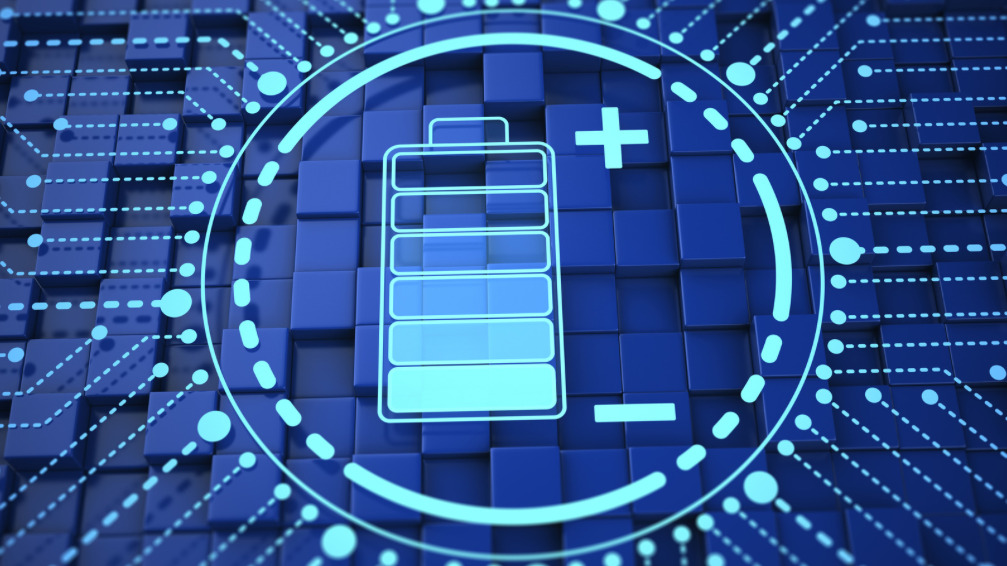
Lithium batteries have helped power society’s shift to renewable energy, serving as the industry standard for everything from electric vehicles to grid-scale energy storage. Scientists are continually looking for sustainable non-lithium battery alternatives because lithium-ion batteries come with safety risks and environmental consequences in their production.
Lithium batteries are the most widely used rechargeable batteries in today’s technology. They power devices ranging from smartphones to electric cars. These batteries are composed of individual lithium-ion cells and a protective circuit board. The history of lithium-ion battery technology dates back to the 1970s when researchers began exploring the potential of lithium as a battery material due to its low electrochemical potential. In the 1980s, Sony introduced the first commercial lithium-ion batteries using lithium cobalt oxide as the cathode material. Over the years, scientists have developed different cathode materials like lithium iron phosphate (LFP / LiFePO4) and lithium nickel manganese cobalt oxide (NMC) to improve the safety, stability, and energy density of Li-ion batteries. Researchers continue to explore new materials and technologies to enhance the performance of battery technology, aiming to increase energy storage capacity and reduce costs.
Here is a look at the challenges of lithium-ion, or Li-ion, and how emerging battery technologies strive to be safer and lower-cost alternatives to lithium batteries while still balancing performance, cost, and environmental impact.
What Are Non Lithium Battery Alternatives?
As demand for sustainable and efficient energy storage solutions rises, researchers and engineers are exploring lithium alternatives. New promising emerging battery technologies include aqueous metal oxide batteries, solid-state lithium batteries, sodium-ion batteries, lithium-sulfur batteries, and flow batteries. These innovative approaches aim to enhance energy density, improve safety, reduce environmental impact, and lower costs, ultimately shaping the future of battery energy storage systems and electric vehicles.
Aqueous Metal Oxide Batteries
Alsym aqueous batteries are a non-toxic alternative to lithium-ion that completely avoids lithium and cobalt and uses water as the primary solvent in the electrolyte and in the manufacturing of the electrodes. Using readily available, inherently non-flammable materials including manganese and other metal oxides, Alsym batteries offer high performance at lower cost and risk than Li-ion.
Solid-State Lithium Batteries
Instead of a flammable liquid electrolyte, solid-state batteries use a solid electrolyte to reduce the risk of fires caused by thermal runaway. Solid-state batteries can potentially pack more energy into a smaller space, making them useful for applications like EVs where more energy translates to more miles per charge.
Solid-state batteries may also exhibit better cycling stability, which is the ability of a battery to maintain its performance and capacity over repeated discharge cycles without significant degradation. They can also operate over a wider temperature range, making them more suitable for extreme environments.
Despite recent advancements in solid-state technology, scientists are still trying to find an electrolyte that simultaneously offers high conductivity, stability, and low manufacturing costs. The most promising solid-state battery chemistries have been difficult to scale up for mass production at an affordable price point, and developers need a cost-effective means of manufacturing the batteries before they can be used commercially.
While solid-state batteries may be safer when it comes to thermal runaway imposed by normal operation, researchers at Sandia National Labs have concluded that they could pose similar risks as traditional lithium-ion batteries when punctured or crushed.
Sodium-Ion Batteries
Sodium-ion batteries are rechargeable batteries that operate similarly to lithium-ion batteries, but use sodium ions (Na+) instead of lithium ions (Li+). The cathode is often made of materials like sodium cobaltate or copper hexacyanoferrate. The anode can be made of materials like hard carbon, soft carbon, or titanium-based compounds.
Sodium-ion batteries are considered a potential solution to the scarcity and cost associated with lithium resources. The technology can be manufactured using existing infrastructure and equipment designed for Li-ion batteries, making it easier to scale up production and integrate sodium-ion batteries into existing energy storage systems. They are also reported to have a lower risk of thermal runaway and a lower environmental impact in the manufacturing process.
Unfortunately, sodium-ion batteries generally have lower energy density than Li-ion batteries and currently have trouble maintaining stable performance over repeated charge and discharge cycles. They typically have longer charging times compared to Li-ion batteries, which can limit their suitability for applications that require fast charging. And because the technology is still in the early stages of commercialization, it will be a while before they are widely available. Sodium metal, like lithium metal, is also highly reactive and flammable and most Na-ion batteries also require a flammable organic electrolyte. Though Na-ion cells may be less energetic than Li-ion, they still pose a significant safety risk.
Lithium-Sulfur Batteries
Some companies are looking into lithium-sulfur (Li-S) batteries as a sustainable alternative to Li-ion. Rather than relying on scarce materials like cobalt, Li-S batteries would benefit from the wider availability of sulfur, making them less dependent on limited resources and cheaper to produce. Li-S batteries also have a theoretical energy density several times higher than that of lithium-ion batteries, storing an equal amount of energy in a more lightweight form.
However, Li-S batteries tend to degrade more rapidly due to poor cycling stability. Sulfur does not have high electrical conductivity to begin with. It also undergoes significant volume expansion and contraction during charge and discharge, resulting in the dissolution of active material and a loss of charge capacity. Additionally, the chemical reaction between sulfur and lithium results in the formation of compounds that reduce Li-S batteries’ efficiency over time.
Further, lithium metal supplants the graphite anode in Li-S batteries. Li metal anodes have a host of other issues associated with dendritic plating, excessive Li consumption in the formation of SEI, and an increased risk of thermal runaway from shorting.
Flow Batteries
Flow batteries, also known as redox flow batteries, are a type of rechargeable battery where energy is stored in liquid electrolyte solutions that are kept in external tanks, as opposed to conventional batteries where the energy is stored by electrodes within the battery cell itself.
Flow batteries consist of two separate tanks of liquid electrolyte solutions. The electrolytes are pumped from these tanks into a cell where they are separated by a membrane. One electrolyte acts as the cathode and the other as the anode. The electrochemical reactions take place in the cell. During the discharge phase (i.e., when energy is being supplied for an external device), electrons are transferred from the anode to the cathode, creating an electric current that oxidizes and reduces the electroactive species in the electrolyte on the respective sides of the cell. During charge, the electroactive species in the anolyte (anode side of the membrane) decreases oxidation state while that of the catholyte (cathode side) increases oxidation state. During the charging phase, an external power source is used to reverse this reaction, replenishing the electrolytes.
Flow batteries have a very long cycle life and minimal degradation over time because the energy is stored in the electrolyte rather than in the battery cell itself. Another advantage of flow batteries is that they can be left completely discharged for long periods without suffering any damage, which is not the case with many other types of batteries. They also have a quick response time.
Flow batteries have some downsides as well. Their energy density is significantly lower than lithium-ion batteries, meaning they take up more space for the same amount of energy stored. This makes them unsuitable for portable applications, or situations where grid storage is needed in urban or suburban areas. They can also be complex and expensive to manufacture and maintain, as the system involves pumps, sensors, and control units to manage the flow of the electrolyte.
Negative Effects of Lithium-Ion Batteries
Even though they are promoted as a way to mitigate climate change, lithium-ion batteries cause damage to the environment during their manufacturing. For instance, every ton of lithium extracted through hard-rock mining results in 15 metric tons of carbon dioxide emissions. Moreover, the technology uses a narrow set of raw materials — lithium, cobalt, and nickel, among others — controlled by a handful of countries in South America, Asia, and Africa.
This far-flung supply chain not only leads to high transportation costs but also results in a number of environmental and ethical issues:
• Lithium mining has been associated with accelerating drought and displacing Indigenous populations in countries ranging from Chile to Serbia.
• Most of the world’s lithium refining facilities are in China, which is notorious for its abundant use of heavily polluting coal.
• Cobalt mining in the Democratic Republic of Congo is known for exploiting child labor, displacing residents, and damaging the environment.
• Nickel mining in Indonesia has contributed to deforestation, soil erosion, and water pollution.
Lithium-ion batteries also pose significant safety risks. Their organic electrolytes have flash points as low as 60 degrees Celsius, and improper use can cause them to overheat. Before a battery cell in thermal runaway actually catches flame, it vents flammable gases such as hydrogen fluoride and carbon monoxide. These toxic vapors can cause an explosion when they ignite, making Li-ion battery fires especially dangerous, even “safer” chemistries like LFP / LiFePO4.
Alsym’s Non Lithium Battery Alternative
Alsym’s non lithium alternative batteries can be manufactured in the same facilities but at a lower cost than lithium-ion batteries, allowing us to take advantage of existing infrastructure and industry knowledge. While other battery technologies must be produced in costly dry rooms and clean rooms and use toxic solvents that require recovery systems, our batteries can be built with less complexity and increased safety.
We’re working to make low-cost, non-flammable batteries available to all. Contact us to find out more about the future of large-scale battery storage technology.